Horizontal Metal Chips Briquetting Machine
Mfano | SL-2000 |
Kipenyo cha briquette | 60-90 mm |
Kasi | 2~3briketi/dak |
Injini | 18.5 kW |
Uzito wa briquette | Aluminium≤2.5ton/m³ |
Mfano | SL-2500 |
Kipenyo cha briquette | 90 ~ 110mm |
Kasi | Briketi 3~5/dak |
Injini | 18.5 kW |
Uzito wa briquette | Aluminium≤2.5ton/m³ |
Sasa unaweza kuwauliza wasimamizi wetu wa mradi kwa maelezo ya kiufundi
Aina ya usawa ya mashine ya briquetting ya chips za chuma ni ya kibiashara vifaa vya vyombo vya habari vya chuma chakavu, ambayo inaweza kutumika sana katika mistari mbalimbali ya uzalishaji wa briquettes za chuma. Vipande vya chuma vya kawaida kama vile chips za alumini, poda ya chuma, shavings ya shaba na chips na aina nyingine za mabaki ya chuma yanaweza kubandikwa kwenye briketi yenye msongamano wa juu kwa usafirishaji rahisi.
Utangulizi mfupi wa mashine ya kuweka briqueting ya chip za chuma kiotomatiki
Mashine ya briquette ya keki ya shavings imeundwa kwa muundo wa mlalo. Inaweza kubana aina mbalimbali za mabaki ya chuma kwa mlalo. Inaweza kukandamiza vipandikizi vya chuma vya punjepunje na unga kuwa keki za silinda za kilo 2-8. Kwa ufanisi wa juu wa kufanya kazi kwa kuchakata rasilimali za chuma chakavu, mashine hii ya briquette ya chip inaweza kutumika sana katika mitambo ya kutupia chuma, viyeyusho vya chuma, sekta ya ujenzi, makampuni ya kuzuia uchafuzi wa mazingira, na mitambo ya usindikaji wa mashine.
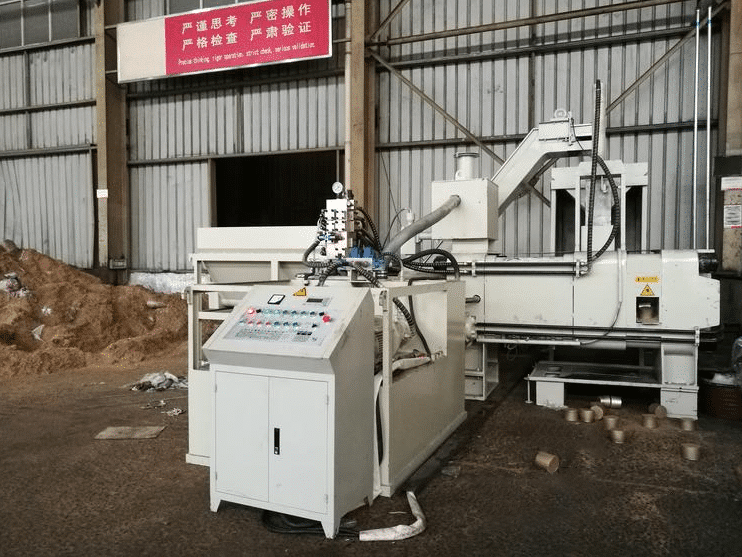
Je, ni vipengele vipi vya mashine ya kutengeneza briquet ya chips za chuma?
Briquetter ya chip ya chuma inaundwa hasa na silinda ya mafuta ya kukandamiza, chumba cha kukandamiza, mfumo wa majimaji, mfumo wa umeme, mfumo wa kudhibiti usalama, na mfumo wa moja kwa moja wa mfuko. Mashine inaweza kuwa na gari la jenereta ya dizeli, inayofaa kwa maeneo yenye usambazaji duni wa umeme.
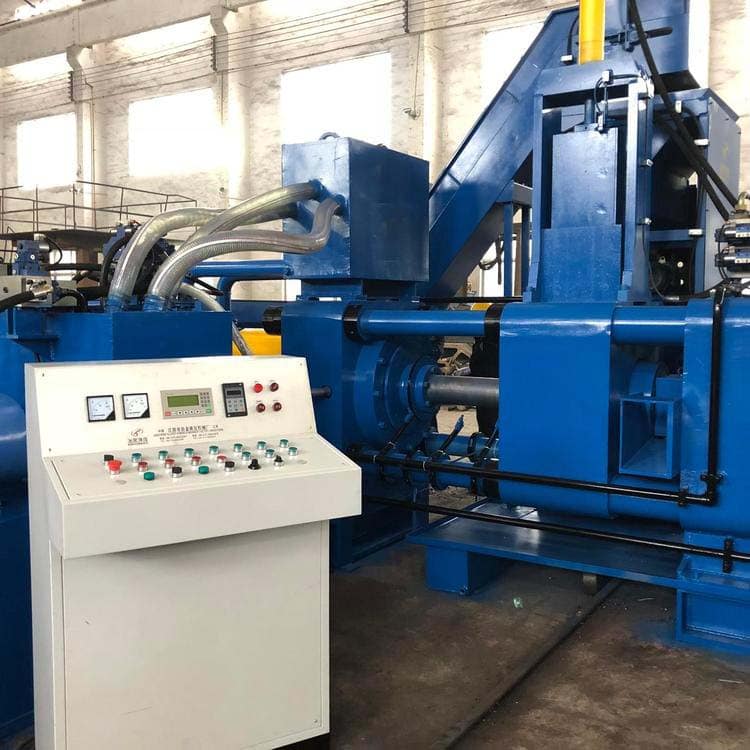
Jinsi ya kuunda mashine ya briquetting ya chips za chuma?
Muundo wa boriti tatu, sita
Mashine ya briquette ya chips za chuma hutumia aina hii ya muundo.
Boriti ya juu na benchi ya kazi ya mashine ya briquetting imeunganishwa kwenye sura iliyowekwa kwa njia ya nguzo, karanga za kufunga, na karanga za kurekebisha.
Usahihi wa sura hurekebishwa na nut ya kurekebisha, ambayo ina nguvu nzuri, rigidity, na uhifadhi wa usahihi.
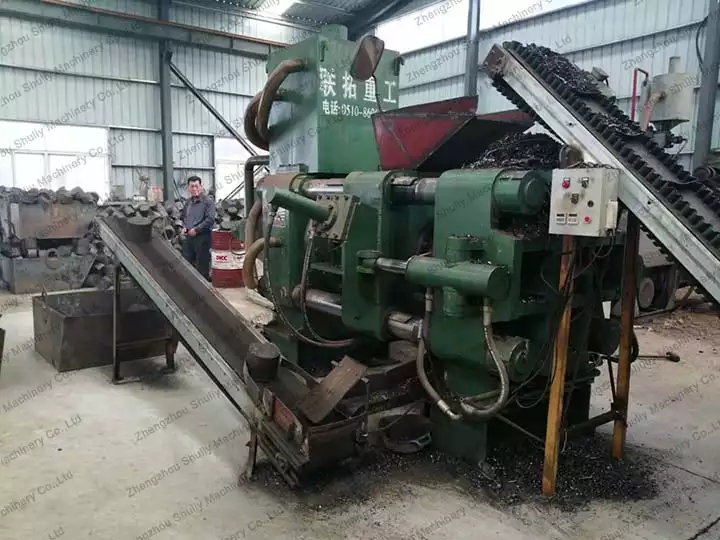
Sahani za chuma zenye svetsade
Boriti ya juu, meza, slider, na vipande vingine vikubwa hutumia mmea huu. Sehemu hizi zimeboreshwa na zimeundwa na kompyuta. Nguvu zake, uthabiti, muundo, na upinzani wa mabadiliko hukutana na viwango vya kimataifa na mahitaji ya matumizi, na sababu ya kutosha ya usalama. Vyombo vya habari vya chuma vya unga hutumia kulehemu kwa kinga ya gesi ya dioksidi kaboni na kulehemu kwa mwongozo wa arc ili ubora wake wa kulehemu uwe wa juu sana na unaweza kuondoa matatizo ya deformation kupitia matibabu ya kuzeeka ya vibration.
Slider ya mashine ya briquetting
Kweli, ni sahani ya chuma iliyo svetsade na muundo wa sanduku. Nyenzo za sleeve ya mwongozo kwenye shimo la mwongozo wa safu nne ni nyenzo za mchanganyiko wa nano-Masi, ambayo ina upinzani mzuri na uhifadhi wa usahihi.
Kwenye ndege ya chini ya slider, kuna T-slots kwa ajili ya ufungaji wa mold.
Boriti kuu ina silinda kuu ya kazi ya mafuta. Kwenye silinda kuu ya kufanya kazi, kuna tank ya mafuta iliyojaa kioevu. Sehemu ya kazi ya mashine ya briquetting ya chips za chuma pia ni sahani ya chuma iliyo svetsade sehemu ya kimuundo, ambayo imeunganishwa na boriti ya juu na kitelezi kupitia safu ili kuunda jeshi.
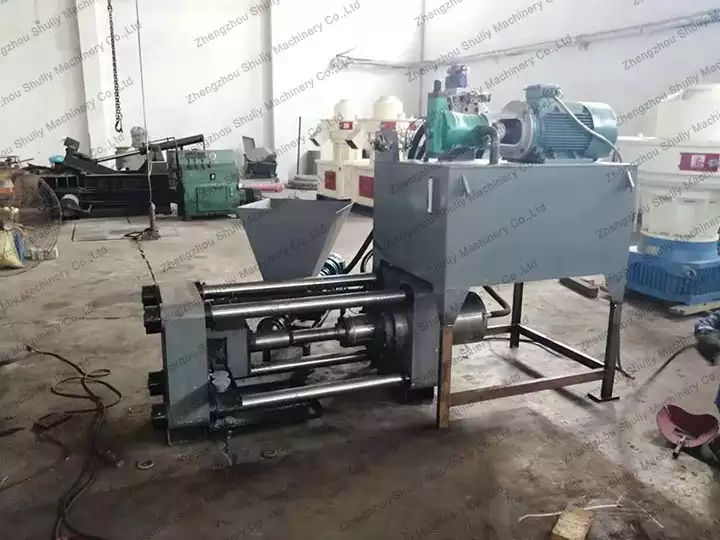
Muundo wa silinda ya shaba
Silinda ya shaba ya mashine ya briquette hutumia muundo wa silinda tano, ambayo hupangwa kwenye shimo la juu la boriti na imefungwa kwa muhuri wa njia mbili. Sehemu ya mwongozo inatibiwa na kulehemu kwa shaba, ambayo imefungwa na ina upinzani mzuri wa kuvaa. Nyenzo za mwili wa silinda ni chuma cha kughushi 45. , Forgings ni daraja la 3 (forgings ni sifa kwa ultrasonic kugundua dosari, na kuzimwa na hasira).
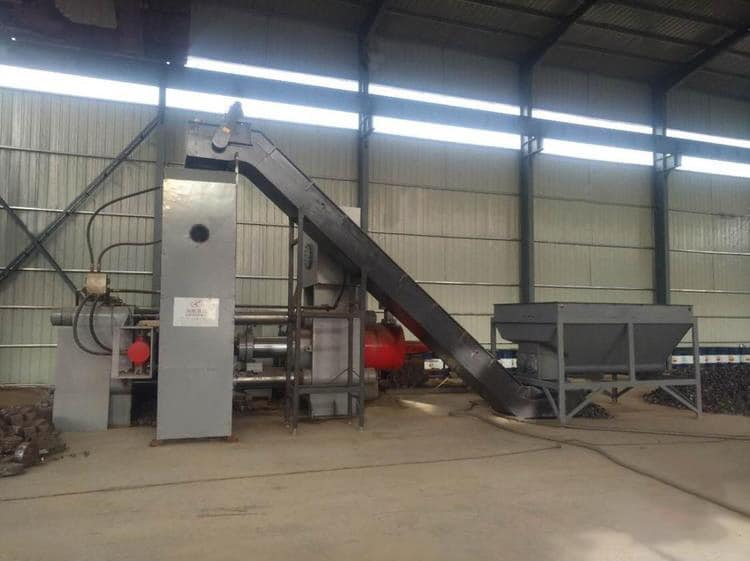
Je, briquetter ya chip ya alumini ya majimaji hufanya kazi vipi?
Mashine hii ya kuweka briquet ya chips za chuma hutumia shinikizo la majimaji linalotolewa na mitungi ya majimaji ili kubana nyenzo.
Wakati wa kazi, mzunguko wa motor unaweza kuendesha pampu ya mafuta kufanya kazi, kutoa mafuta ya hydraulic kwenye tank ya mafuta, kuisafirisha kupitia bomba la mafuta ya hydraulic, na kuihamisha kwa kila silinda ya mafuta ya hydraulic ili kuendesha fimbo ya pistoni ya silinda ya mafuta. kwa longitudinally kubana chips mbalimbali za chuma katika tank nyenzo.
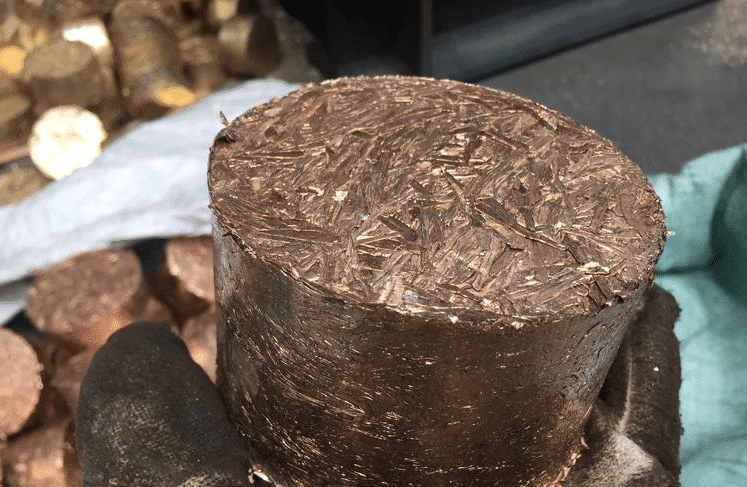
Mutunzaji vidokezo vya mashine ya briquetting ya chuma ya usawa
- Inashauriwa kutumia mafuta ya hydraulic ya 32 na 46 ya kuzuia kuvaa kwa mafuta ya majimaji yanayotumiwa wakati mashine inafanya kazi. Tumia joto la mafuta kati ya 15 hadi 60 ℃.
- Mafuta ya majimaji huchujwa kwa ukali kabla ya kuruhusiwa kuongezwa kwenye tangi. Maji ya kazi yanapaswa kubadilishwa mara moja kwa mwaka, na wakati wa uingizwaji haupaswi kuzidi miezi mitatu.
- Ikiwa mashine haitumiwi kwa muda mrefu, uso wa kila sehemu unapaswa kusafishwa na kuvikwa na mafuta ya kupambana na kutu.
- Slide ya mashine ya briquette ya chuma inapaswa kujazwa na mafuta ya kulainisha mara kwa mara, uso wa nje wa safu unapaswa kuwekwa safi mara kwa mara, na mafuta yanapaswa kuingizwa kabla ya kila kazi. Kipimo cha shinikizo kinapaswa kuchunguzwa kila baada ya miezi sita.
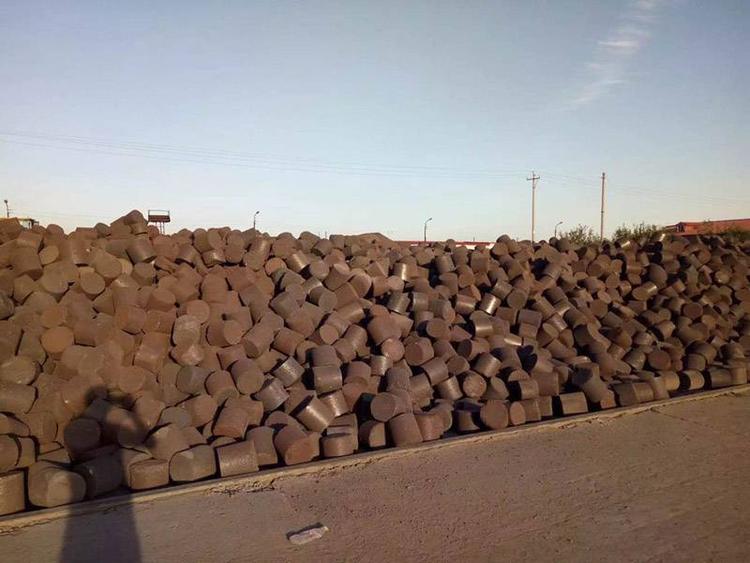
Maelezo ya kiufundi ya vyombo vya habari vya briquette ya chuma
Mfano | Kipenyo cha briketi (mm) | Kasi (briketi/dakika) | Motor (kW) | Uzito wa briquette (tani/m³) |
SL-2000 | 60~90 | 2~3 | 18.5 | Aluminium≤2.5 |
SL-2500 | 90~110 | 3~5 | 22 | Aluminium≤2.5 |
SL-3150 | 100~110 | 3~5 | 30 | Chuma, chuma cha kutupwa≤5.5 |
SL-3600 | 100~130 | 3~5 | 30 | Chuma, chuma cha kutupwa≤5.5 |
SL-5000 | 120~160 | 3~5 | 22×2 | Shaba, shaba≤7.0 |
SL-6300 | 120~200 | 3~5 | 30×2 | Shaba, shaba≤7.0 |