Maintenance of hydraulic aluminum can baler
The hydraulic aluminum can baler directly cold presses various metal scraps through hydraulic pressure so that the scrap metal is convenient for storage, transportation, and recycling. The processing capacity of aluminum can balers is very large. Through scrap metal baling, the storage space of scrap metal can be reduced, saving up to 80% of stacking space, reducing transportation costs, and being conducive to environmental protection and waste recycling.
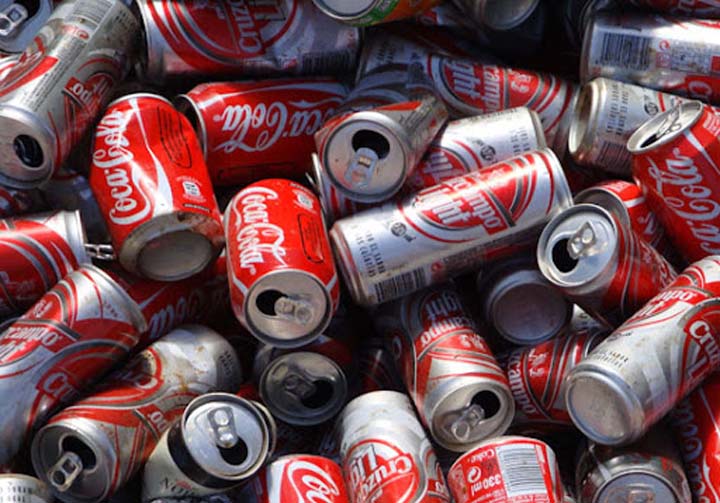
The main components of the hydraulic aluminum can baler
- Box body. The box body of the aluminum can packer is welded by thicker steel plates, which is the stacking area of metal scrap.
- Motor. The motor is the power unit of the aluminum cans baler, which converts electrical energy into mechanical energy.
- Oil pump. The oil pump of the aluminum can baler machine can convert the hydraulic oil from a static state to a moving state.
- Oil tank. The hydraulic cylinder is the part where the metal baler squeezes the waste in the bin.
- Control valve group. The control valve group mainly controls the forward and backward movement of the piston in the cylinder of the hydraulic aluminum tank baler.
- Hydraulic oil. Hydraulic oil is the blood for the normal operation of the aluminum tank baler machine.
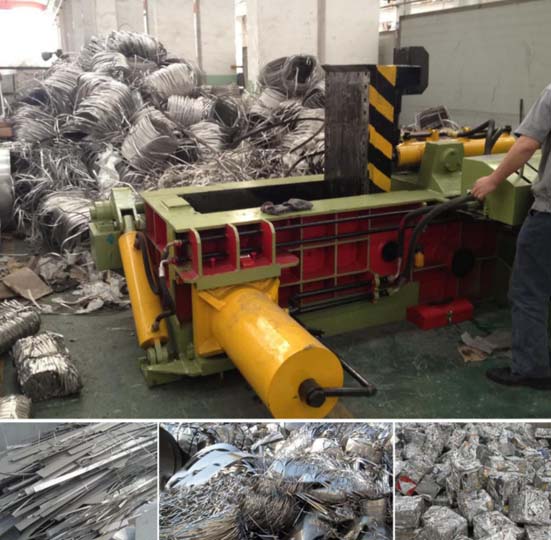
How to maintain the hydraulic aluminum can balers?
- The hydraulic oil added to the oil tank of the aluminum can packer should use high-quality anti-wear hydraulic oil. This hydraulic oil must also go through a strict filtering process, and it should maintain a sufficient amount of oil. When the amount of oil is insufficient, add it in time to avoid damage to the machine.
- The oil tank of the hydraulic baler needs to be cleaned regularly and replaced with new oil. Generally speaking, the hydraulic oil needs to be changed every six months. The used hydraulic oil can be reused after being filtered.
- The lubrication of the hydraulic aluminum tank baler should use high-grade lubricating oil, and the lubricating oil should be added at least once per shift.
- If there are sundries in the bin, clean up in time to prevent the accumulation of sundries from affecting the operation of the bin and the entire machine.
- When the machine is found to be seriously damaged or oil leaking, it should stop running immediately, and analyze the cause and failure, and do not force the machine to run.