Wie wählt man die Tonnage und Entlademethode einer Schrottballenpresse aus?
Die Schrottballenpresse ist die gängige Ausrüstung zum Recycling aller Arten von Schrottabfällen. Sie kann eine große Anzahl von Metallabfällen in Blöcke pressen, was für den Transport von Metallabfällen praktisch ist und Lagerraum spart. Nur durch die Wahl der richtigen Metallballenpresse kann die Recyclingeffizienz von Metallabfällen verbessert werden.
Wie wählen Benutzer also die richtige Schrottballenpresse aus? Wie ermitteln Sie, welche Tonnage an Metallballenpressen Ihren Anforderungen entspricht? Was ist der Unterschied zwischen verschiedenen Entlademethoden der Schrottballenpresse?
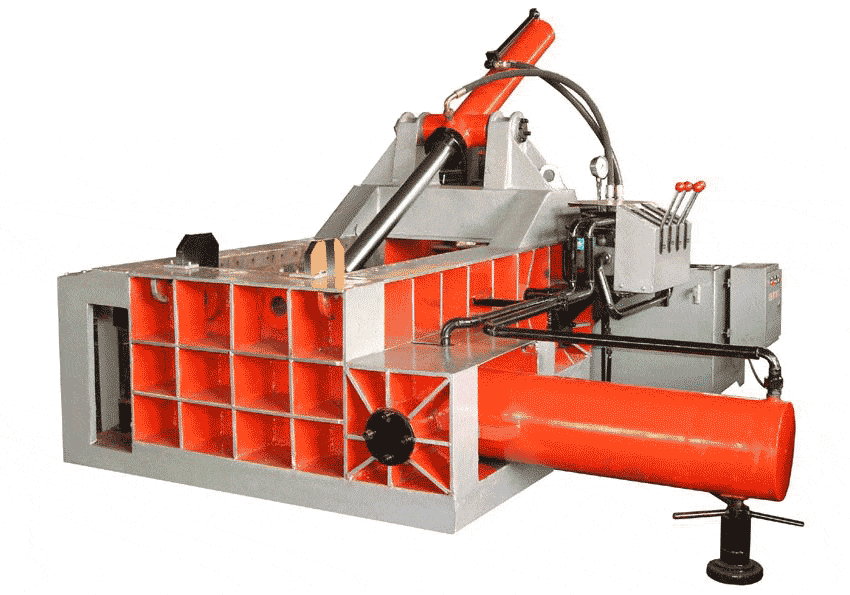
Das Prinzip der Wahl der Tonnage der Schrottballenpresse
Wie wählt man die Tonnage der Metallballenpresse? Im Allgemeinen sollten Kunden die Tonnage der ausgewählten Metallballenpresse entsprechend ihren eigenen Produktionsanforderungen bestimmen. Dies liegt daran, dass je größer die Tonnage ist Ballenpresse für MetallabfälleJe höher die Verarbeitungseffizienz und desto größer die Verarbeitungskapazität.
Wenn der Ausstoß des Kunden groß ist, wählen Sie daher eine Metallballenpresse mit großer Tonnage, und wenn der Ausstoß klein ist, entscheiden Sie sich für eine Schrottpressmaschine mit kleiner Tonnage.
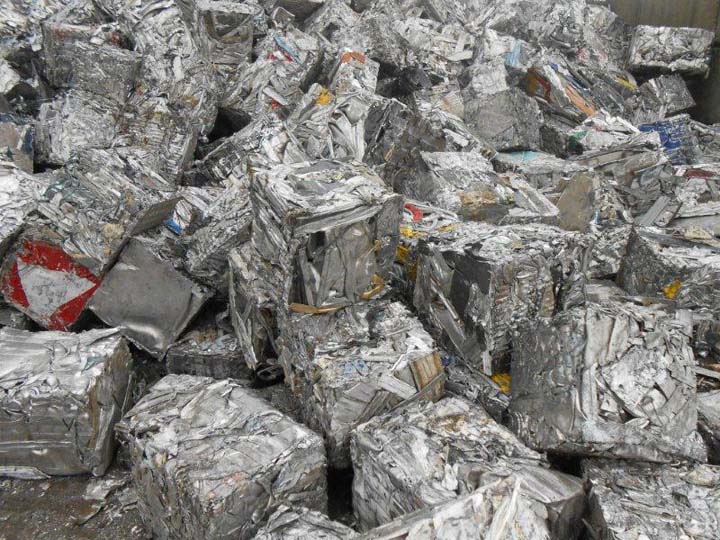
Gängige Tonnageauswahlschemata für Metallballenpressen
- Für 5-10 Tonnen wählen Sie den Typ SL-Y81-1250.
- Für 10–20 Tonnen wählen Sie den Typ SL-Y81-1600.
- Wählen Sie SL-Y81-2000 für 20–30 Tonnen.
- Wählen Sie SL-Y81-2500 für 30–50 Tonnen.
- Für 50–70 Tonnen wählen Sie den Typ SL-Y81-3150.
Zweitens müssen Kunden auch anhand ihrer Rohstoffe bestimmen, welche Art von Metallballenpresse sie benötigen. Für die Verarbeitung von leicht zu Ballen zu pressenden Metallabfällen ist die Leistung des Ballenpresse aus Metall ist hoch. Im Gegenteil, die Produktion von Rohstoffen, die sich nicht leicht pressen lassen, ist gering. Daher ist die Auswahl der Tonnage von Schrottballenpressen sehr wichtig, und eine schlechte Auswahl führt zu hohen Maschinenkosten und geringer Effizienz.
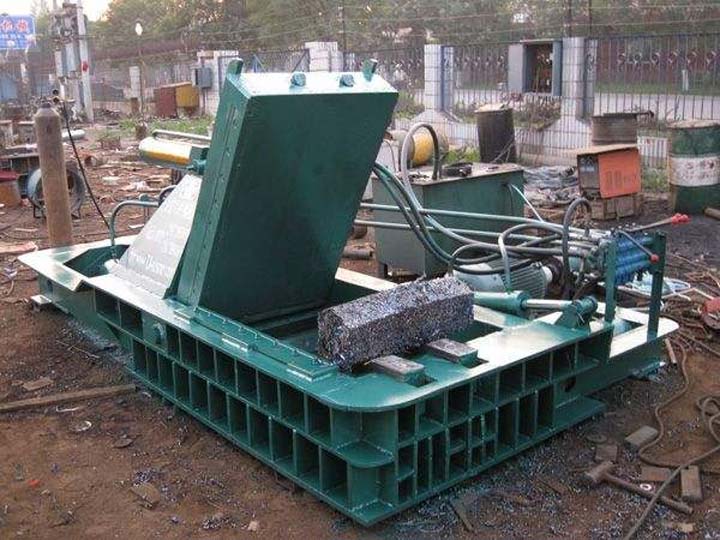
Wie wählt man die Entlademethode einer Schrottballenpresse?
Die am häufigsten verwendeten Austragsmethoden für Metallballenpressen sind Seitenauswurf, Frontauswurf, Seitenextrusion und andere Austragsmethoden.
Wenn das Rohmaterial des Kunden aus Aluminium besteht, empfehlen wir dem Anwender, die Frontauswurf- oder Seitenauswurfmethode zu verwenden. Denn die Art und Weise, wie das Material gewendet wird, verformt die Metallballen und beeinträchtigt das Aussehen der Metallballen.